

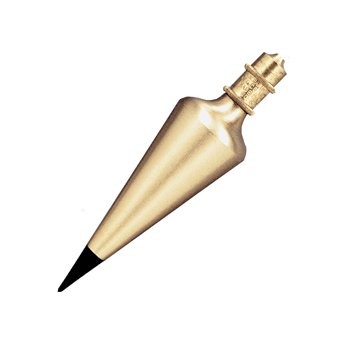
For this short run of high quality production the use of ‘permanent’ metal moulds and the gravity die casting method would have been ideal. Each has a cartouche for the name of the recipient, blank for this pair so perhaps they are from old, non-presented stock. The bookends have a tapered design that makes them ideal for their purpose in addition to being easy to strip from a mould. The symbolic part of the design includes an hour glass between a pair of wings, illustrating well how time flies when working for a good employer. The tray is approximately 150x105mm (6 x 4”), weighs a fairly hefty 900g (2lb) and has a gilt lacquer finish.Ĥ761 A pair of bookends specially cast by Bridgeport Brass Co for presentation to employees completing 25 Years Service. Motor Castings a speciality’, ‘This casting is just as it leaves the sand.’ The centre pillar again includes a risqué design. The underside of the tray has a smooth finish and cast-in lettering that is vastly better than that of the oval example. The bottom of the tray has a decorative scroll. In the background is a tree and a post carrying the message ‘Rubbish can be shot here’. It is 125mm (5”) square.ħ899 The Autumnal design of the rectangular tray shows a female gardener wearing a headscarf and navigating a pile of leaves with her wheelbarrow forming a high relief foreground together with its handles, a spade and hazel broom. Jay and Son Ltd., still working in Oak Street, Norwich. Weight 370g.ħ82 A striking central bird motif showing a jay in the centre of a cast brass ashtray was perhaps an obvious but excellent choice made by brassfounders L. Intriguingly, there is no mention of the name of the industry, hopefully it can be recognised? American, 58 x 50 x 67mm high. Height approx 44mm (1¾”).ġ209 A paperweight commemorating 'Industrial Outing 1939' in the form of a dog of spaniel-like appearance screwed to a rectangular base with iron weighting and a green baize under-surface. The ends are left well fettled and smooth. It appears to be a one-piece casting with an open interior showing a central vertical mould parting line. It is well made a replica of the Post Office House in Clachan, North Uist, Scotland by a skilled founder.

By 1930 they were at Crane Building, 836 South Michigan Avenue, Chicago, Illinois and had manufacturing plants for cast brass valves, plumbing supplies and other products at Chicago, Bridgeport, Birmingham, Chattanooga, Trenton and North Tonawanda, N.Y.ħ026 On a similar but simpler theme is this cast brass souvenir from the 1938 Empire Exhibition held in Glasgow. The company was formed by Richard and Charles Crane in Chicago as R T Crane & Bro. The top notice board reads, in relief, ‘ R T Crane, Brass and Bell Foundry’ and the base has an impression reading ‘1855 Crane Co 1925’. The separate base has edging representing pipes with corner bends and is secured to the hut by two screws. There are various ways in which this could have been made but clues are covered by a coating of a lasting matt brass finish. The casting technique for the hut is intricate because of the presence of re-entrant features that mean that it was not a simple two-part mould. If the surface finish of a souvenir was slightly defective and needed attention it was more likely to be scrapped rather than rectified.ġ228 This superb sand cast brass reproduction of a wooden office hut is in two parts, the base and the hut itself. The design usually required a demonstration of foundry skills such that very little fettling was to be used. If wording was to be inserted in the casting, it had to be very carefully moulded. The casting surface had to be excellent on all faces so use of the finest grade of moulding sand was essential. The pattern had to be made very carefully and finished to a perfect surface finish. A decision to make a celebration souvenir would call up top skills to supplement normal procedures. Most castings then needed to me machined to some extent to ensure that faces would mate with assembled components and were also frequently drilled and tapped for securing screws. After being cast and knocked out of the sand, items were usually ‘fettled’ by cutting off the runners, risers and breathers that had let the liquid metal in uniformly and the air out accordingly and dressing the surface as needed. Once made and used for the first time, patterns were identified and kept in store in the pattern loft as carefully as might be until needed again. Traditional brass foundries would cast their products by pouring molten brass to solidify to shape in sand moulds with each shape needing its own wooden pattern.
